Guest Article Series – Cirplus – Part 2
A closer look at the Circular Plastics Economy – Episode #1
Will the petrochemicals embrace the change or fight it?
By Christian Schiller, Co-Founder and CEO at Cirplus (Contact via eMail)
The Petrochemicals (aka plastic manufacturers, such as BASF, Dow Chemical, Borealis etc.) are in a bind: with a supply chain built around extracting petroleum and selling ever more new (aka “virgin”) plastic, the advent of genuine circular economy efforts and all the talk of “keeping plastic in the loop” fundamentally defies their century old business model. The problem is straightforward: if a ton of plastic once sold and processed gets reused and eventually recycled in multiple loops, such recyclates will replace more and more virgin plastic. If you can reuse and recycle a ton of plastic multiple times, why buy a new one?
Sure, the idea of 100% closed-loop recycling remains a mere vision in the world of 2020 and for years to come. But even an increase to 25% or 50% of the world’s plastic demand covered by recyclates will mean a massive shift in value creation, away from the oil and petrochemical industry to an entirely different industry: the waste and recycling industry. In numbers: a 25% share of the European plastic converter demand (in 2018 levels) for recycled plastic would mean 12.8 million tons of recyclates. A market potential of at least 15 billion Euros.
And the demand for plastic worldwide is still rising — as is plastics’ relative share in the overall crude oil refinement. The International Energy Agency (IEA) projects a 33% share by 2030 and nearly 50% petrochemical share by 2050 (plastic being the most prominent petrochemical product).
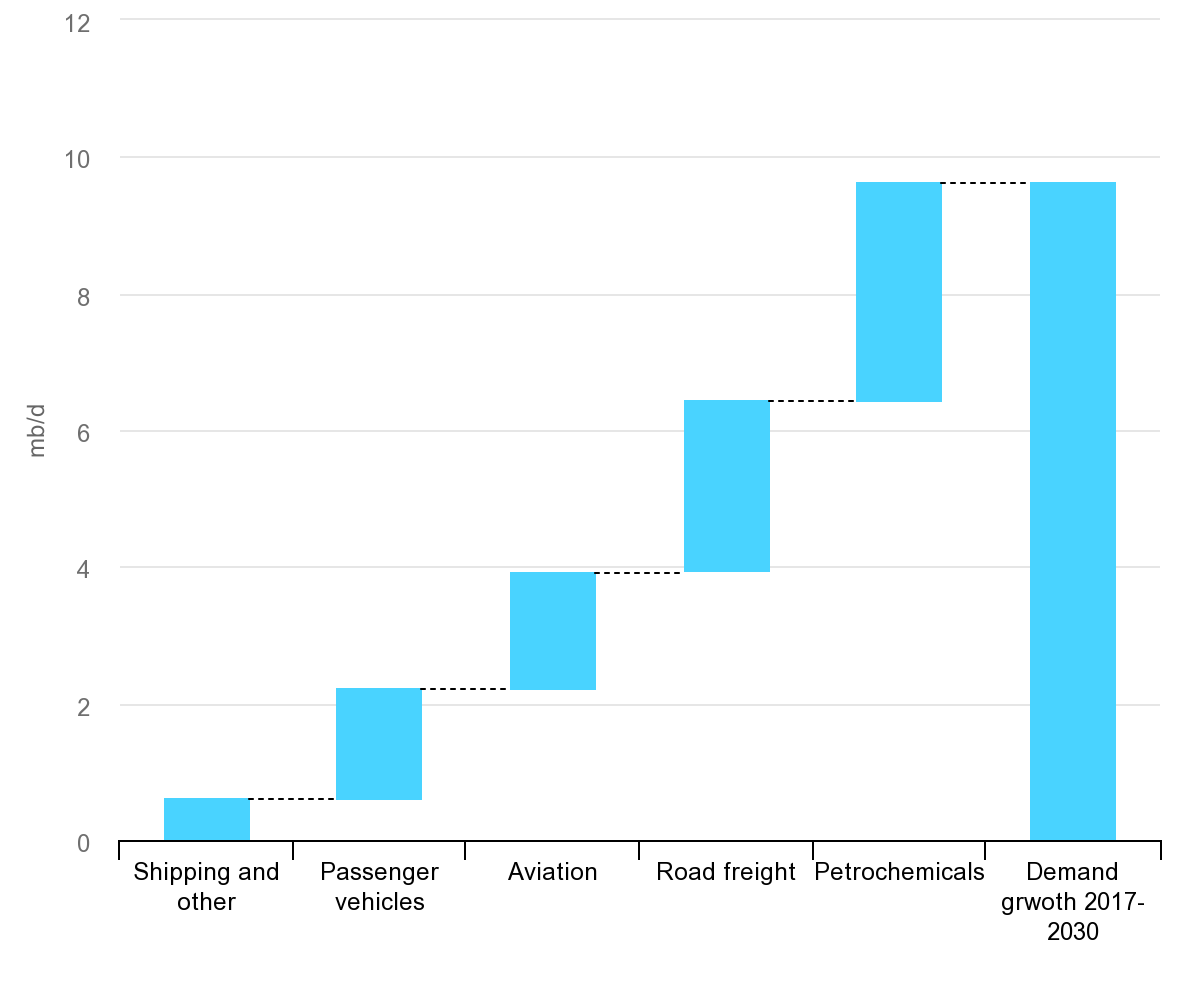
Source: IEA
In short: plastics is a gargantuan market — and one of the reasons why the petrochemicals turn to different strategies to counter the threat of losing business. And turn to new strategies they must: For the global push away from combustion engine towards cleaner forms of transportation (electric, hydrogen etc.) will mean a significant drop in demand for fossil fuels coming from passenger vehicles and road freight. With a key market for their products going down, big oil producers and petrochemicals see plastics as a way to outgrow the decline of transportation markets.
You might wonder: Why such rise in absolute and relative importance of plastics? Isn’t the world trying to move away from this polluting material? What about all the microplastic and the marine littering?
More wealth means more plastic consumption — and more waste
The reality is: not quite so fast. There is a simple rule: When economies grow wealthier, so does their per capita consumption of plastics. And ever more developing nations are climbing up the wealth ladder, contributing to unfettered demand growth of this valuable material. Not least in times of Corona: a recent survey among German plastic converters showed that packaging and medical plastics production is reaching capacity limits due to changing consumer behaviors during the pandemic (i.e. more single-use plastics, more consumption at home, more online shopping etc.). It seems like talking the talk of sustainability is cheap, walking the walk is the hard thing. But with public pressure and regulators calling ever more forceful for an end of the plastic crisis, the message is being heard at the highest levels of the industry.
So, what do you do when you are the Cercei Lannister of Petrochemicals, wanting to maintain or even improve your market share in plastics and your sustainability footprint at the same time? Answer: If you can’t prevent the change, embrace it. (Sure enough, there is also intense lobbying efforts ongoing on national and international levels to keep the status quo. But it is this author’s belief that change in the plastic production value chain is inevitable, even despite the severe effects Corona has on world economies. These efforts will be addressed separately).
Petrochemicals turning into plastic recyclers?
The pioneers of the industry decide to become a recycler on their own merit with the idea of continuing to supply the world with premier grades of virgin and recycled plastics. After all, the plastic converters (i.e. the companies buying plastic as raw material and converting it into whatever plastic product you can think of, such as packaging, consumer goods, automotive parts etc.) have established long-standing relationships with the virgin plastic suppliers or their distributors, they speak a similar language of chemistry and polymers. In contrast, mechanical recyclers speak the language of waste. Not so easy to bridge the gap. That is why some petrochemicals decide to build up their own recycling capabilities.
But not all recycling efforts are created equal: For example, German petro-giant BASF goes down the alley of chemical recycling, having created an entirely new business unit called ChemCycling in 2019. While the process itself is not new, the economics have not worked out in the past, which is why companies like Covestro (formerly part of Bayer AG) stopped their expeditions into the chemical recycling lands, for example of compact discs, only to renew their efforts in light of the recent push for sustainability. Environmental and profitability concerns remain at the forefront of the discussion, with critics calling it a “distraction, not a solution” to the plastic crisis.
Austria-based Borealis AG ventures down a different alley: that of mechanical recycling. With the acquisition of mtm plastics in Germany (2016) and Eco-Plast in Austria (2018), this petro-giant put its chips on an alternative — and somewhat competing — form of recycling. Both projects serve to seize market and technology opportunities for mechanical recyclates, giving answers to the questions: with sufficient investment and marketing efforts and the backing of a large petrochemical, can mechanically recycled plastics from post-consumer and post-commercial waste feedstock truly replace virgin material at industrial scale?
Both chemical and mechanical recycling technologies have their merits and none can be outright judged as “not economical” or “not ecological” without a look at the alternative treatments of plastic waste. This is because plastic products at the end of their lifecycle are complex and so is their respective market demand. However, if the goal is to close the loop with the least amount of energy requirements and environmental impact, there is a strong argument for a “recycling hierarchy” of mechanical over chemical recycling. Ultimately, a differentiated environmental impact assessment is needed per plastic product at the end of its “use-phase”.
For example: with the first generations of wind power plants going out of service in Germany, what happens to their carbon fiber reinforced rotor blades? Today, there is no recycling stream readily available for this valuable resource at industrial scale. Only an individual analysis can tell if it makes sense to recycle it and with which method.
One thing is for sure: simply disposing it and letting it rot in nature is not an acceptable solution. Nor is the continued incineration of plastic waste — in times where we are trying to get off energy generation from fossil fuels, notably carbon, it remains one of the great absurdities of the circular plastics economy to tout incineration as an acceptable form of treating plastic waste — often euphemistically cloaked as “energy recovery” or “thermal recycling”. It simply means to burn a petroleum-based product to generate heat and energy, emitting large quantities of CO2 and toxic pollutants. And with it, the valuable polymer chains of the plastic literally dissolve in “thin air” instead of being reused multiple times over as a recyclate.
Diversity of plastics hinders more effective recycling
The diversity of grades even within the same category of plastics further adds to the sluggish movement, even resistance, of the petrochemicals to make plastics more easily recycable. An industry insider told me that just within the category of polypropylene (PP), one of the standard plastics, more than 1500 grades are commercially available on the market today. The same applies to other plastic types. Add to that the long list of additives and masterbatches — needed to achieve the desired performance of the specific plastics use case — and you can increase plastics’ complexity almost ad infinitum.
That is a severe problem for recycling because it requires ideally clean and highly sorted waste streams. Yet sorting technology is stuck in the past century for lack of markets for recyclates (and thus lack of investments). So while today’s sorting technology can deliver a roughly homogenous plastic waste stream, the diversity of the virgin grades in the same plastic category make the recycling process more cost-intensive, i.e. less competitive to virgin plastic. This is because the recycler needs to invest more effort into homogenizing the output material. (Please note: this problem described here is different to the issue of multi-layered materials and complexity of plastic compounds enriched with plasticizers, flame-retardants and other additives. This will be addressed at a later stage, together with contamination of plastic waste.)
And as of June 2020, there is no commercially available sorting technology or waste stream management system that could sort plastic waste according to the original virgin grades of the same type of plastics.
Sure, one could call for “simplification of virgin grades” to make recycling easier. But a diversified product range, backed by intellectual property protection, in our market economies usually mean market shares and commercial advantages. Will petrochemicals so easily turn to reduced complexity of their grades if this is fundamentally opposed to their market strategies? And not to forget: not all diversification is driven by pure marketing strategy, but also by market demand. Customers of plastic resins expect a very specific performance of the particular plastics. The chemical engineers at petrochemicals do a terrific job in catering to these market needs. It therefore remains an open engineering question if product manufacturers (aka brand owners or OEMs) and their plastic converters would, or even could, demand to build their products with a simplified inventory of virgin plastic grades in the future so that the petrochemicals would reduce complexities of their plastic grades and thus facilitate the transition to a world with better recycling.
But let us assume for a moment that with enough public pressure and consumer demand, the petrochemicals are reigning in the complexity of their product portfolio and only produce easy-to-recycle plastic grades and compounds and technology improves to guarantee homogenous sorted waste streams: The elephant — or rather dragon — is yet to enter the room. And it will stay with us all through the entire series. And that is the feedstock security.
The ultimate challenge: feedstock security
No matter from which angle you look at recycling: a recurring challenge remains the feedstock sourcing, i.e. how to get your hands on stable supply of more or less homogenous waste feedstock? This question occupies both mechanical and chemical recyclers alike, less so the incinerators. Because you can only run a recycling plant at a profit if your raw material is reliable and economically to procure. The idea that one can simply throw all types of mixed plastic waste into a big black (mechanical or chemical) recycling box and out comes a fresh new plastic ready for reuse is an illusion. Thus feedstock security is a significant challenge for all stakeholders in the circular plastics value chain considering to build up their own recycling capacities. We will revisit the issue in greater detail when we turn to the waste management and recycling industry.
One thing is certain: a Lannister always pays its debt and the petrochemicals — once truly pushed towards more sustainability — do not shy away from big challenges. Their technology has always been technology at the frontier of what is possible, extracting ever more of this valuable material from crude oil. If the full force of their monetary and technological power is geared towards keeping plastics in the loop — starting with making plastics more easily recyclable — I have no doubt in my mind that true recycling of plastics will become the new norm and not an exotic outlier that is too often still sneered at in the world of oil giants and petrochemicals.
And pressure begins to build up equally from another great player in the Game of Thrones of Circular Plastics to whom we turn in the next episode: the Brand Owners and OEMs.
We have asked cirplus, the Climate-KIC supported recyclates marketplace, to give us an insight into the plastics market from a start-up’s perspective. In the upcoming article series, Christian Schiller, Co-Founder of cirplus, is taking a closer look at the challenges of the circular plastics economy these days. The full series will be published in the following weeks. Join our LinkedIn group to stay tuned!